We go beyond the ordinary
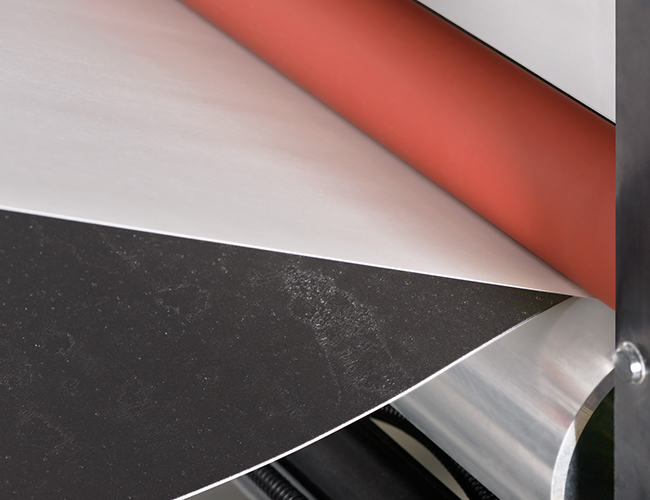
KMB is the partner of choice if you require more than just "standard". From experience we know that surprisingly simple and practical solutions are often found when someone from the outside looks for one. Since we’re not blinded by routine we know what is technically feasible, useful and expedient. You also benefit from having an expert in all areas at your side: we develop, coat and punch. Depending on your requirements and run size, we complete your order by machine or manually, always keeping an eye on the cost effectiveness for you.
We process all common materials from transfer adhesive tapes, scrims or films to foam adhesive tapes. We even manufacture stamped parts from butyl in excellent quality. We manufacture using our own products though we also process materials from various other manufacturers too such as ATP Alltape, Avery, 3M, and many more. We are proficient in handling combinations of different adhesive and coating processes too.
Do you need punched parts made of non-adhesive materials? KMB is the right partner for that too. It’s always worth getting in contact!
Real-life examples
We not only create perfect adhesive solutions and punch them into shape, upon request we can also apply adhesives to your injection-moulded parts, join components together perfectly or laminate and emboss your prefabricated elements.
Depending on requirements, the work is carried out either using our large range of machinery or manually. We attach particular importance to precision and meeting deadlines as well. Below are some examples from the past:
Sector: Automotive industry
The task:
An automobile manufacturer equips its vehicles with anti-kick film to prevent the paint on the side rail from being damaged when entering and exiting the vehicle. The films were to be punched to the exact shape and finished with a metallic foil for optical enhancement. The anti-kick film should be permanently self-adhesive for easy application.
The solution:
As the anti-kick film is exposed to both mechanical forces (impact, shock, abrasion) and physical influences (cold, heat, moisture), selecting the right adhesive was the greatest challenge for the specialists at KMB. In addition, the film has to adhere securely to the car body even after many years. After numerous tests and in close cooperation with the manufacturer KMB's technicians, developed a solution that met all requirements. The specifications of the design department were also implemented 1:1: A metallic foil with the lettering of the vehicle type was incorporated into the anti-kick film for aesthetic purposes.
The result:
The film was used in numerous vehicles and models and fulfilled its purpose as per the manufacturer's specifications.
Sector: Electrical industry
The task:
A well-known German electronics group was looking for a practical and cost-effective method to equip plastic signs for fuse boxes with a double-sided adhesive surface.
The solution:
KMB found a way to cleanly and accurately fit the signs on the panels with double-sided adhesive film in one work step. This was much more time-saving than applying the punched parts individually. And the customer also benefited from KMB's expertise in selecting the appropriate adhesive and carrier material.
The result:
KMB developed a solution that not only perfectly fulfilled the functional requirements but also impressed in terms of cost effectiveness.
Sector: Automotive industry and others
The task:
Brand emblems, e.g. intended to be mounted on the vehicle’s wheel hubs are finished in such a way that they a) are easy to attach b) withstand mechanical stress (car washes), climatic factors (frost, heat, moisture) and chemical influences (road salt, detergent) by means of strong adhesion.
The solution:
After extensive testing in its laboratory, KMB used an adhesive that met all requirements. It was applied to the carrier material which was then punched into shape. A grip tab was also integrated to ensure quick and safe removal.
The result:
The design department was also delighted with the result: By gluing the back of the transparent material with a metallic foil which had adhesive on both sides, the trademark emblem was further visually enhanced. What’s more, this also eliminated the time-consuming printing process – a welcome bonus.
Sector: Automotive industry
The task:
A punched adhesive film was required for the precise and quick installation of seat heaters in passenger cars. One of the requirements was that the backing paper had to be able to peel cleanly from the existing adhesive for fast and smooth subsequent processing.
The solution:
Together with an adhesive manufacturer, KMB optimised the backing paper on both sides of the adhesive in such a way that it can initially be easily removed from one side while remaining completely adhered to the second backing paper. At the same time, however, it can be removed relatively easily from the second backing paper. The adhesive can be thus further processed as desired. Additional holes punched into the material ensure that the heat of the subsequently integrated heating elements can penetrate into the seat and does not accumulate under the material.
The result:
The KMB development team drew on its experience to use the most suitable adhesive in addition to the perfectly fitting carrier. The installation process was, as requested by the client, thus optimised without affecting functionality.
What’s more: We’re also happy to take on commission work for you in the event of personnel or machine bottlenecks.